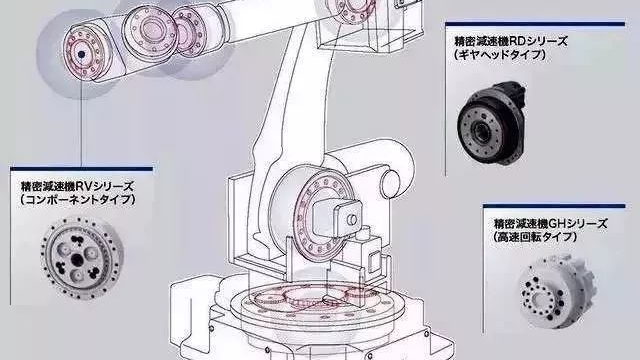
Maintenance of Industrial Robots
The use of industrial robots in manufacturing industry is increasing, especially in harsh conditions or with high work intensity and sustainability requirements. Plus the low rate failure, makes robots widely recognized. However, even the design of industrial robot is standardized, integration is quite high and the failure rate is low, routine inspections and preventive maintenance must still be carried out regularly. Common robots like: tandem articulated robots, Cartesian coordinate robots, Delta parallel robots, scara robots, automatic guided trolleys, etc., the maintenance in this article is mainly for articulated robots. Maintenance of industrial robot body General maintenance 1) Clean the manipulator Regularly clean the base and arm of the manipulator; High-pressure cleaning equipment can be used, but direct injection into the robot should be avoided; If the manipulator is protected by…